From valve types and regulations to materials and functions, everything you need to know
Voids that control, regulate, or direct flow within a system or process are what valves are at their most fundamental.
They frequently have a variety of traits that serve to specify their best use.
However, there are probably stainless steel valves accessible to aid whether you’re wanting to manage flow, ensure safety in a system that is piping liquids, solids, gases, or anything in between.
Valves serve a variety of purposes, such as:
Depending on the state of the valve, varying the flow
controlling the pressure and flow within a piping system
regulating the flow direction inside a pipe system
reducing the flow rates through a pipe system
reducing pressure or vacuum in a pipe system to increase safety
Valve Opening Methods Explained
Although numerous valves achieve the same objectives, the mechanical details can differ.
A valve’s total performance is affected by how it opens and closes, as well as by how much control you have over the flow and how rapidly the valve can work.
The majority of valves fall into one of three groups:
Multi-Turn valves: These valves can be compared to a screw or a piston. The plug, plate, membrane, or other regulating impediment is moved into the pipe’s path and blocks access when you turn the handle. These can have higher or lower differentials depending on the valve, allowing you to open or close them at different speeds.
Quarter-turn valves: A full range of motion is available with a 90-degree handle turn on quarter-turn valves. They are therefore perfect in circumstances when the speed of action and ease of opening or closing are more crucial than precision.

Consider the manner of actuation in addition to the mechanical motion a valve involves. Valve types often fall into one of three groups:
Manual Valves : These valves use handwheels, hand levels, gear wheels, or chains to activate and are typically regulated by hand.
Actuated Valves: These valves provide remote control and automation for high-precision or large-scale applications and are frequently connected to electric motors, air or pneumatic systems, hydraulic systems, or solenoids.
Automatic Valves: Some valves open when a particular flow requirement is satisfied. Examples include pressure release valves opening when an overpressure condition is recognised or check valves closing during backflow.
Common Valve Types and Their Applications
Valves have a variety of traits, benchmarks, and classifications that help you understand their intended uses and anticipated performance. One of the simplest methods to sort the vast selection of valves available and find a good fit for a project or process is through valve designs.
Common types of valves include:
Ball Valve

These valves, which often have quick-acting 90-degree turn handles, use a ball to control flow to enable simple on-off control. Operators often agree that butterfly valves are quicker and simpler to use than gate valves.
Butterfly valves
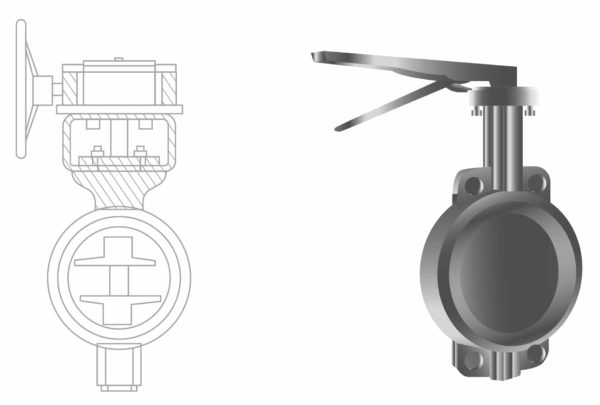
Thanks to its wafer-type design and compact size, the butterfly valve is a quick-acting rotary motion valve that works well in small places. Butterfly valve bodies come in a wide variety of designs.
Check Valve

These self-activating valves, which are used to stop backflow, automatically open when media flows through them in the desired direction and close when the flow changes.
Gate Valve

Gate valves, one of the most prevalent valve types, start and stop the flow via linear motion. Usually, they are not utilised to control flow. They utilised in the fully open or closed states instead.
Knife Gate Valve

The knife gate valve has a thin gate controlled by linear action that may cut through materials and produce a seal, and it is typically used to regulate the flow of media containing solids.
These valves are appropriate for usage with grease, oils, paper pulp, slurry, wastewater, and other media that would hinder the operation of other valves, while they are not suitable for high-pressure installations.
Globe Valve

Globe valves are frequently used in control activities that modulate the output. usually comes in three body types: the T-body (as in the example above), the Y-Pattern, and the Angle body.
Needle Valve

Needle valves derive its name from the tip on a conical disc utilised within. They are frequently employed in tiny diameter piping systems when delicate, accurate flow control is required.
Pinch Valve

Pinch valves have a linear motion and are frequently used for handling solid materials, slurries, and liquids containing suspended solids. In order to isolate the media, pinch valves frequently have an interior sleeve.
Plug Valve

These valves regulate flow by turning a valve handle a quarter turn quickly. They use tapered or cylindrical plugs. When a tight shutdown is required, they offer some of the greatest ratings and are dependable in high-pressure or high-temperature settings.
Pressure Relief Valve

These spring-automated valves are used to help increase safety and will aid in restoring a system to the desired pressure during over-pressure incidents.
As an alternative to design, valves may also be categorized by function.
Common functional names and the common design categories that correspond to them include:
Isolation Valves: Ball, butterfly, diaphragm, gate, pinch, piston, and plug valves
Regulation Valves: Ball, butterfly, diaphragm, globe, needle, pinch, and plug valves
Safety Relief Valves: Pressure release and vacuum relief valves
Non-Return Valves: Swing check and lift check valves
Special Purpose Valves: Multi-port, float, foot, knife gate, and line blind valves
Valve Sizing Explained: Keeping Things Flowing
Although they might only take up a little amount of space in your piping system or process, valves can account for a sizable fraction of the design and construction costs. They also significantly affect the overall effectiveness of the system and long-term expenses.
Choosing the right valve size is crucial for cost optimization as well as for guaranteeing reliable, accurate, and safe functioning.
The valve’s overall size should be taken into account before everything else, including its physical dimensions, internal size, and flow rates (CV).
Costs may increase if you select a valve that doesn’t fit correctly in the available space. A system failure or inaccurate flow control can result from selecting a valve that does not offer the ideal flow rate.
For instance, if your valve is too narrow, it could lower downstream flow while increasing upstream backpressure. The flow control rapidly decreases as you move away from fully open or totally closed if the valve is too large.
Make sure to take your needs into account while selecting the right size, taking into account both the connector diameter and the valve’s overall flow rate. While some valves have great flow, some restrict flow and raise pressure.
This means that occasionally a larger valve needs to be installed in order to account for flow than the adapter diameter alone might suggest.
Valve End Connections: Crucial To Proper Fit And Operation
After sizing and design, it’s crucial to think about valve end connections.

The most obvious takeaway from this is that you should select an end connection that works with your plumbing, but there are functional aspects of common end types that could make one valve better suited to your needs than another.
Common valve connections and ends include:
Screwed or Threaded: Utilised frequently in instrument connections or sample points
Flanged: The most typical ends for use with piping
Butt Welded: Utilised frequently in high-pressure or high-temperature activities
Socket Welded: Used frequently on tiny bore pipework where threaded connections are not allowed
Wafer and Lug: Used frequently for small valves put in systems with little room
Valve Materials: Providing Security And Durable Performance
The materials your valves are comprised of may be a crucial factor in maintaining safe functioning and lowering maintenance and replacement costs over the course of your operation, depending on your intended purpose.
In a variety of processing environments, such as those involving corrosive media (like chemicals, saltwater, and acids), environments with stringent sanitation standards (like food and beverage manufacturing and pharmaceuticals), and processes involving high pressure or high temperatures, stainless steel valves are excellent choices.
It is frequently preferable to choose a valve made of a non-sparking material, such as brass, bronze, copper, or even plastic, if you are processing solvents, fuels, or volatile organic compounds (VOCs). Internal (wetted) trim pieces should be tested for chemical compatibility in addition to choosing the right body material. Elastomers in your valve should be assessed for their chemical compatibility as well as any pressure and temperature restrictions.
Valve Standards: Meeting Compliance And Regulatory Concerns
You can discover that valves need to follow specific standards to satisfy legal requirements for safety, hygienic problems, or other issues depending on your planned purpose.
The number of standard organizations and prospective rules is too great to discuss in detail, however, some common generic standard organizations are as follows:
CSA Group (CSA)
The American Society of Mechanical Engineers (ASME)
The American Society for Testing Materials International (ASTM International)
The Manufacturers Standardization Society (MSS)
The American National Standards Institute (ANSI)
The International Organization for Standardization (ISO)
The Public Health and Safety Organization (NSF)
NACE International (NACE)
The American Petroleum Institute (API)
American Water Works Association (AWWA)
Industry-specific norms should also be taken into account.
According to industry, important standards bodies include:
ASHRAE Valve Standards
ASME BPVC Valve Standards
ASSE Valve Standards
ISA Valve Standards
NFPA Valve Standards
SAE Valve Standards
Conclusion
Making the appropriate valve selection for your project may seem difficult. However, you may quickly narrow down your selections to find the ideal valves for your needs by starting with generic criteria, such as valve design, valve size, and valve actuation mechanism.
Read More :
What is Sensitization in Austenitic Stainless Steel? : Sensitization in austenitic steel refers to the process of making steel more resistant to corrosion by increasing its resistance to corrosion-inducing environments.
Understanding the Applications & Uses of Duplex Stainless Steels : Duplex stainless steels belong to the stainless steel family. These are referred to as duplex grades because their metallurgical structure comprises of two phases, austenite and ferrite, in approximately equal quantities.