What is a Butterfly Valve?
A butterfly valve is a type of valve that is widely used in industrial and commercial applications to regulate the flow of fluids or gases. The valve’s name comes from the wing-like shape of its disc, which is mounted on a shaft that runs through the center of the valve body.
Butterfly valves are designed to be lightweight, compact, and easy to operate, making them popular in many industries. They are often used in HVAC systems, water treatment plants, chemical processing plants, and power generation facilities.
Image –
The valve’s disc is positioned perpendicular to the flow direction when fully closed. When the valve is opened, the disc rotates a quarter-turn to align with the flow, allowing the medium to pass through the valve. This simple design allows for fast and efficient flow control, making butterfly valves ideal for use in high-capacity systems.
One of the benefits of butterfly valves is that they require very little maintenance. They have few moving parts and do not require lubrication or other routine maintenance. However, they may not be suitable for use in high-pressure systems or those that involve abrasive materials, as the disc may wear out quickly.
Butterfly valves are available in numerous types and designs, each rated for specific temperature, pressure, and flow requirements, to cater to the demands of pipeline systems dealing with gases and liquids.
Types of Butterfly Valves
There are several types of butterfly valves, each designed to suit specific application requirements. Some of the most common types of butterfly valves are:
1. Wafer Butterfly Valve
Wafer butterfly valves are installed between two pipe flanges and secured using long bolts across the valve body. The valve body may or may not have flange holes outside the valve body. O-rings and gaskets are placed on both sides between the valve body and the pipe flange to create a strong seal.
While wafer butterfly valves have an economical connection design, they cannot be used as isolation valves or in end-of-line service. Maintenance on either side of the valve requires shutting down the entire pipeline.
It is important to note that wafer butterfly valves, like some other types of butterfly valves, are not suitable for high-temperature applications. This is because the valve body may expand, leading to increased stress on the valve bolts and potential failure.

2. Lug Butterfly Valve:
Lug butterfly valves are positioned between two pipe flanges using bolts that pass through threaded inserts or lugs protruding outside the valve body. The valve is supported by two separate sets of bolts on each side of the valve, and no nuts are used in either lug. This enables the valve to be installed in an end-of-line service or to become an isolation valve. The design also enables dismantling on one side of the valve without affecting the other, which reduces downtime during maintenance.
However, it is important to note that the valve body also carries an additional load due to the weight of the pipeline. Furthermore, the pressure rating of butterfly valves is typically reduced when installed in an end-of-line service, as the absence of a downstream flange can cause the media to deform the seat and push past the disc and seat seal. This may cause problems and limit the valve’s effectiveness in such applications.
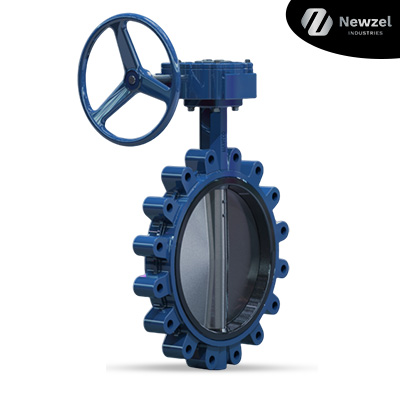
3. Zero Offset Butterfly Valves (Resilient Seat Butterfly Valves)
Concentric butterfly valves, also known as zero offset butterfly valves, have a stem that passes through the centerline of the disc, which is centered in the seat and valve body. When closed, the valve body, seat, and disc lie concentrically, and the disc can rotate 360° on the central axis. In a fully-open position, the flow is divided into two halves on either side of the disc, which becomes parallel to the flow. A significant advantage of this type of valve is that the flowing media does not contact the valve body since the seat covers it.
The zero offset butterfly valve requires a resilient soft seat, which relies on the seat’s flexibility and deformation during sealing. This causes the disc edges to slide onto the seat, resulting in full friction during operation, reducing the valve’s service life. Additionally, since the seat must be made from a polymeric or elastomeric material, the design is limited to lower pressure and temperature ratings.
Zero offset butterfly valves are commonly used in liquid and gas pipelines with pressure and temperature ratings of up to 250 psi and 400°F, respectively.
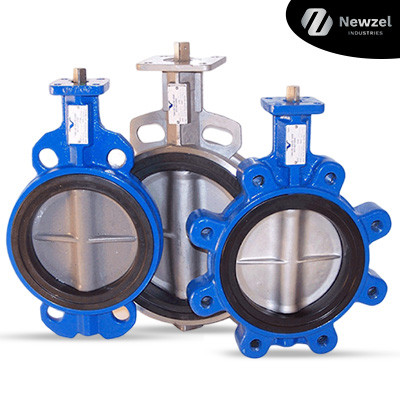
4. Double Offset Butterfly Valve (High-Performance Butterfly Valves)
Double offset butterfly valves have a stem axis that is first offset behind the centerline of the seat and body (first offset), and then further offset from the vertical centerline of the valve (second offset). When the disc opens, the seat lifts from the seal, reducing friction during the first and last 10 degrees of valve opening and closing. This design results in a smoother valve operation, better sealing capability, and longer service life than zero offset butterfly valves.
Similar to zero offset butterfly valves, double offset butterfly valves utilize a soft seat. However, they are capable of withstanding higher pressures and temperatures in liquid and gas pipelines and are available in moderate pressure and temperature ratings.
Double offset butterfly valves are commonly used in water purification, wastewater treatment, HVAC, and fire protection systems, such as fire sprinklers. For increased temperature resistance, a layer of metal backs the soft seat, reducing the amount of soft seat material used.

5. Triple Offset Butterfly Valve
Triple offset butterfly valves have three offsets: the first two are the same as those in the double offset butterfly valves, while the third offset is an angular offset in the body sealing cone axis. This design ensures that the valve has zero friction during opening and closing, as there is no contact between the seat and the disc. Instead, the seat and disc only make contact during full valve closure. This also acts as a mechanical stop to prevent the disc from rotating further.
Unlike zero offset and double offset butterfly valves, triple offset butterfly valves use metal seats that can withstand high temperatures and fluid pressures. These seats provide reliable sealing to prevent any fluid from escaping the valve. Due to their robust design, triple offset butterfly valves have longer service lives compared to their counterparts.
Triple offset butterfly valves are well-suited for applications that involve high-pressure and superheated steam, high-temperature liquids and gases, and corrosive chemicals, which cannot be handled by butterfly valves with soft seats. These valves find wide use in industries such as power generation (e.g., as on-off valves for boilers), oil and gas processing, chemical manufacturing, pulp and paper manufacturing, and offshore pipelines.
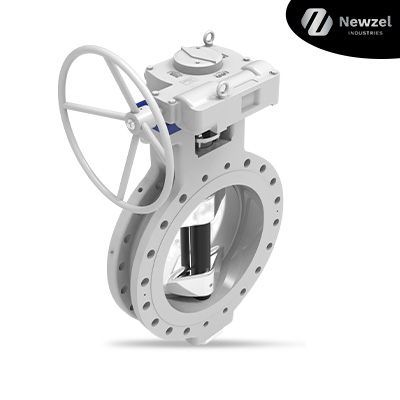
6. Double-Flanged Butterfly Valve
Double-flanged butterfly valves feature two flanges located on each side of the valve body that are designed to match the dimensions of the pipe flanges. This results in a robust attachment using two sets of bolts and nuts to support the valve on each side. These valves are commonly used for larger sizing in the field of butterfly valves.

7. Butt-Weld Butterfly Valves
Butt-weld butterfly valves are a type of butterfly valve that is welded directly to the piping system. The valve body is inserted between two pipe flanges, and the flanges are welded together along with the valve body, resulting in a permanent and leak-proof joint. Butt-weld butterfly valves are typically used in high-pressure and high-temperature applications, as they provide a more robust and secure connection than other types of butterfly valves. They are commonly found in industries such as oil and gas, chemical processing, and power generation.

8. Top Entry Butterfly Valves
Top entry butterfly valves have a distinctive design that enables them to be repaired without the need to disassemble the pipeline. This is achieved by easily removing the valve bonnet from the valve cavity to access the valve stem and butterfly plate. As a result, top entry butterfly valves can be repaired or replaced quickly, minimizing downtime.

The butterfly valve may be a “non-wetted” or “wetted” valve:
Non-wetted valves are designed with a valve body and stem that are lined with plastic or elastomeric materials, such as rubber or Teflon. This lining isolates the valve from the flowing media, allowing the valve to be constructed with materials that have lower corrosion resistance.
In contrast, wetted valves have their valve body and stem exposed directly to the flowing media.
Butterfly Valve Uses
Butterfly valves are used in a wide range of applications, including controlling the flow of fluids in pipelines, tanks, and other containers. Some common uses of butterfly valves include:
- Water supply and treatment systems : Butterfly valves are used in water supply and treatment systems to regulate the flow of water and other fluids.
- HVAC systems : Butterfly valves are used in heating, ventilation, and air conditioning (HVAC) systems to regulate the flow of air and other gases.
- Chemical and petrochemical processing : Butterfly valves are used in chemical and petrochemical processing plants to control the flow of chemicals and other fluids.
- Power plants: Butterfly valves are used in power plants to control the flow of steam and other fluids.
- Food and beverage processing : Butterfly valves are used in the food and beverage industry to control the flow of liquids and gases in various processing stages.
- Pharmaceutical processing : Butterfly valves are used in the pharmaceutical industry to control the flow of liquids and gases during the manufacturing of drugs and other pharmaceutical products.
- Oil and gas processing : Butterfly valves are used in oil and gas processing plants to regulate the flow of fluids during the extraction, processing, and transportation of oil and gas.
- Fire protection systems : Butterfly valves are used in fire protection systems to control the flow of water and other fire-suppressing agents.